Through the collaborative efforts of the entire team, Kanri Soft has transformed operational dynamics, ensuring:
Transforming Factory Operations through Innovative Software Solutions
Overview
Client Overview
Kanri Soft is a leading software producer, specializing in enhancing lean management across all organizational levels. Their product streamlines information exchange between the machinery and humans to enable optimization of production processes. The company’s mission focuses on raising awareness for production process management potential and blockers, through a user-friendly, integrated data platform. Their digital manufacturing management system combines data acquisition, processing, and visualization tools, providing managers with instant, reliable operational insights. This integration facilitates real-time bottleneck identification and informed decision-making, leading to process optimization and resource utilization improvement.
Technologies:
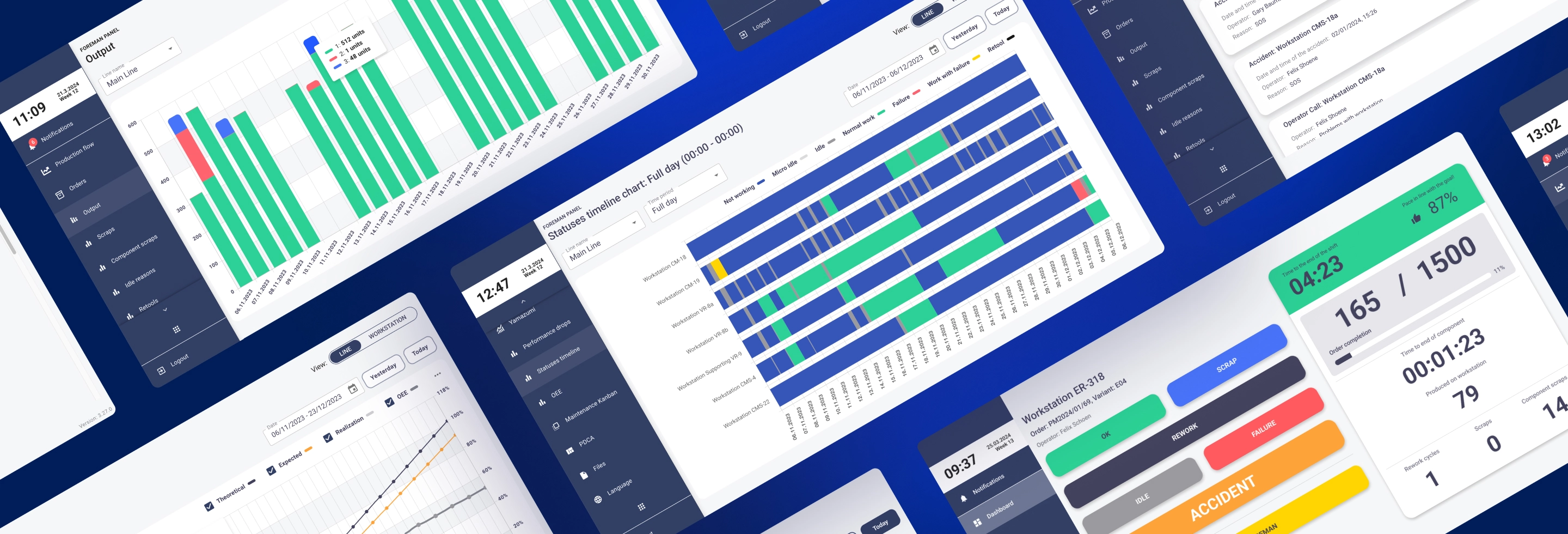
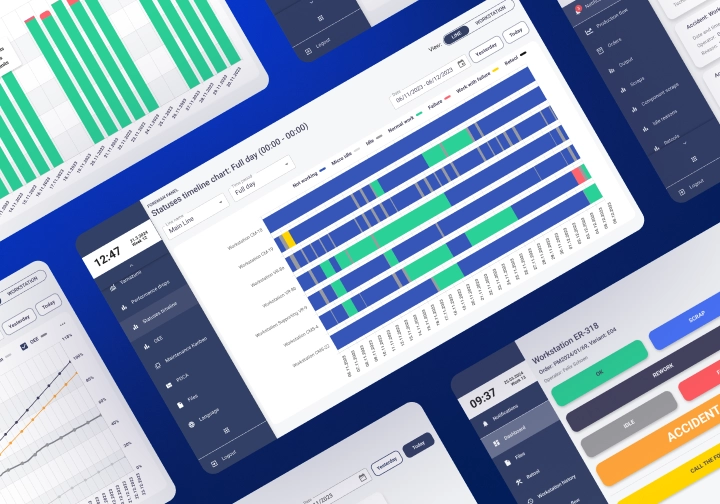
Client’s Business Need
Factories seek comprehensive solutions to enhance manufacturing efficiency and streamline production processes, benefiting from cost efficiency.
Kanri’s client required an optimized information flow, ensuring essential data from production machines was efficiently gathered, processed, and delivered to all stakeholders, from operators to management. They needed a system supporting lean management principles, enabling all organizational levels to actively participate and benefit. The demand for a system offering real-time monitoring of machine conditions and production metrics was critical, providing instant insights for swift, proactive decision-making.
The solution had to effectively identify and reduce waste and inefficiencies, streamlining production while being environmentally conscious. It was essential for the system to be flexible and customizable, accommodating diverse manufacturing environments and client needs, with options for both on-premises and cloud hosting. Lastly, the business required a scalable solution, capable of evolving and expanding its functionalities to areas like HR, payroll, and supply chain management.
The Challenge Approach
The approach to the challenge involved meticulous research, user-centered design, collaborative development, and innovative technological application, all aimed at creating a scalable and efficient solution tailored to the nuanced needs of the manufacturing sector.
In-depth Research
The team dedicated significant effort to understanding the day-to-day operations of manufacturing companies. This involved engaging with various factory personnel, including machine operators, foremen, mechanics, and shift supervisors, to gain insights into their needs and perspectives.
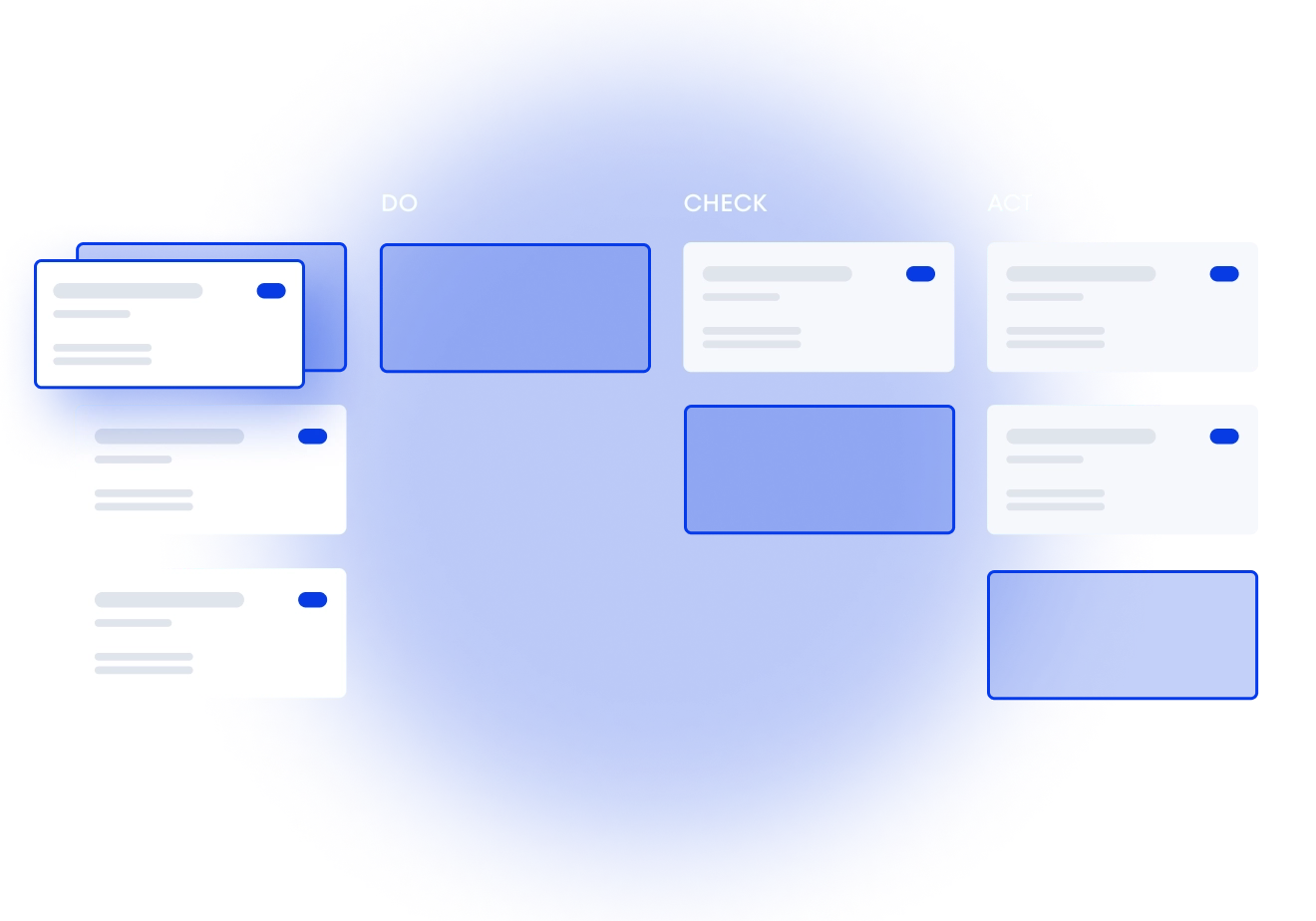
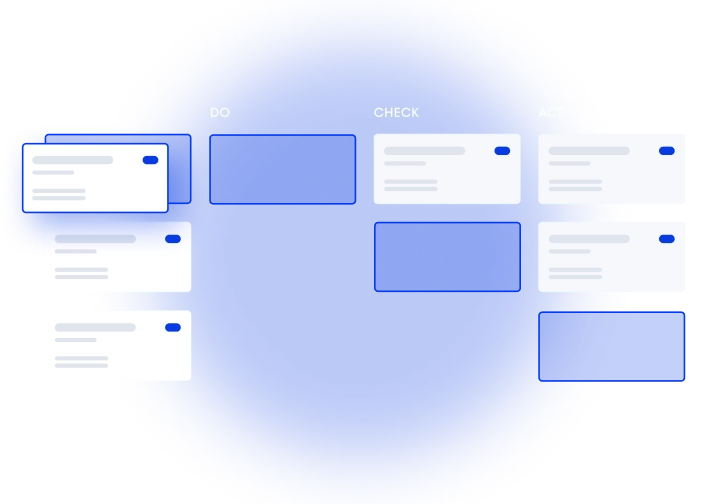
Flexibility & Industry Digitalization
Recognizing the forefront of industry digitalization and the automation of lean processes, the approach required adaptability and a readiness to implement cutting-edge solutions tailored to the evolving landscape of the manufacturing sector.
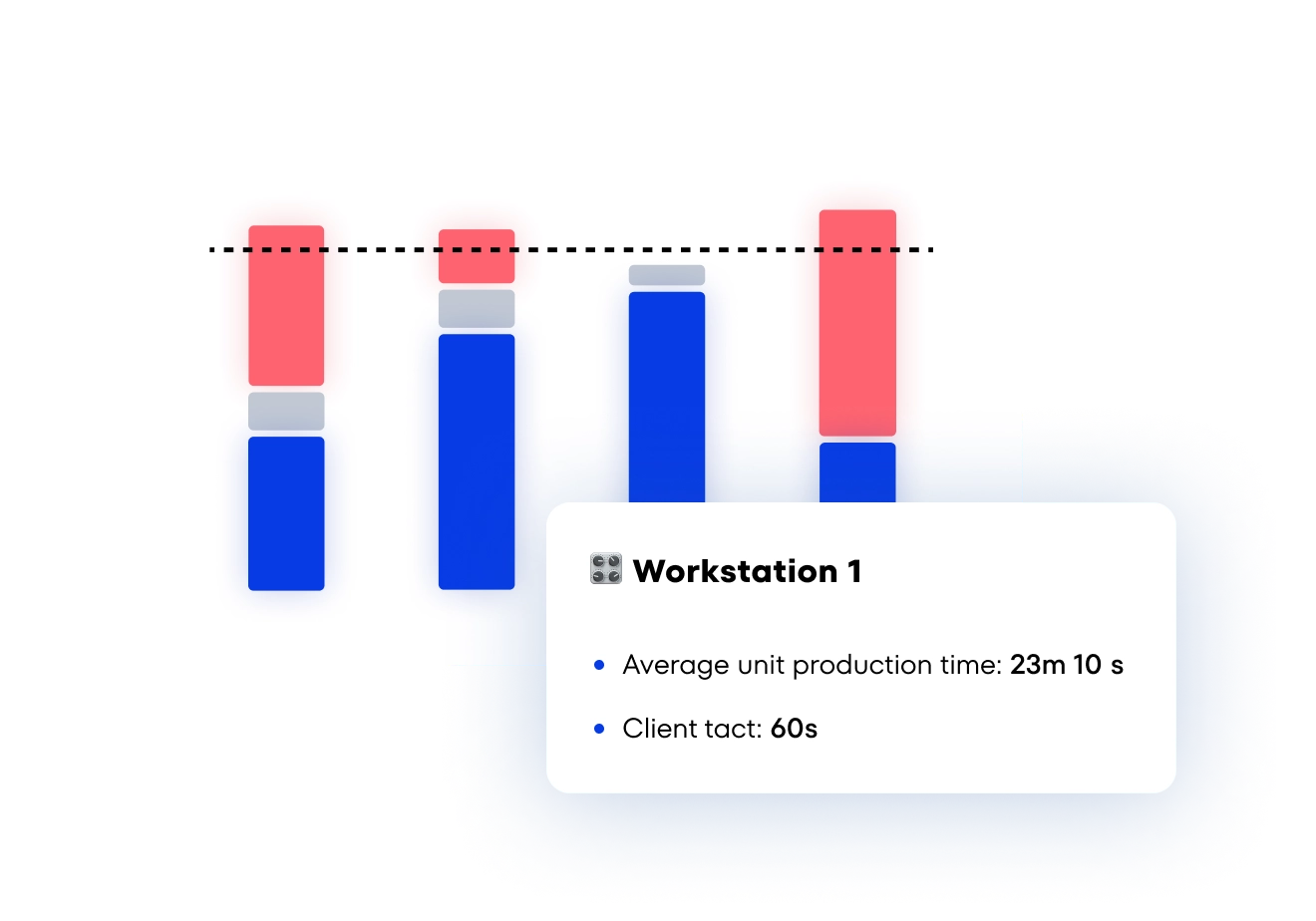
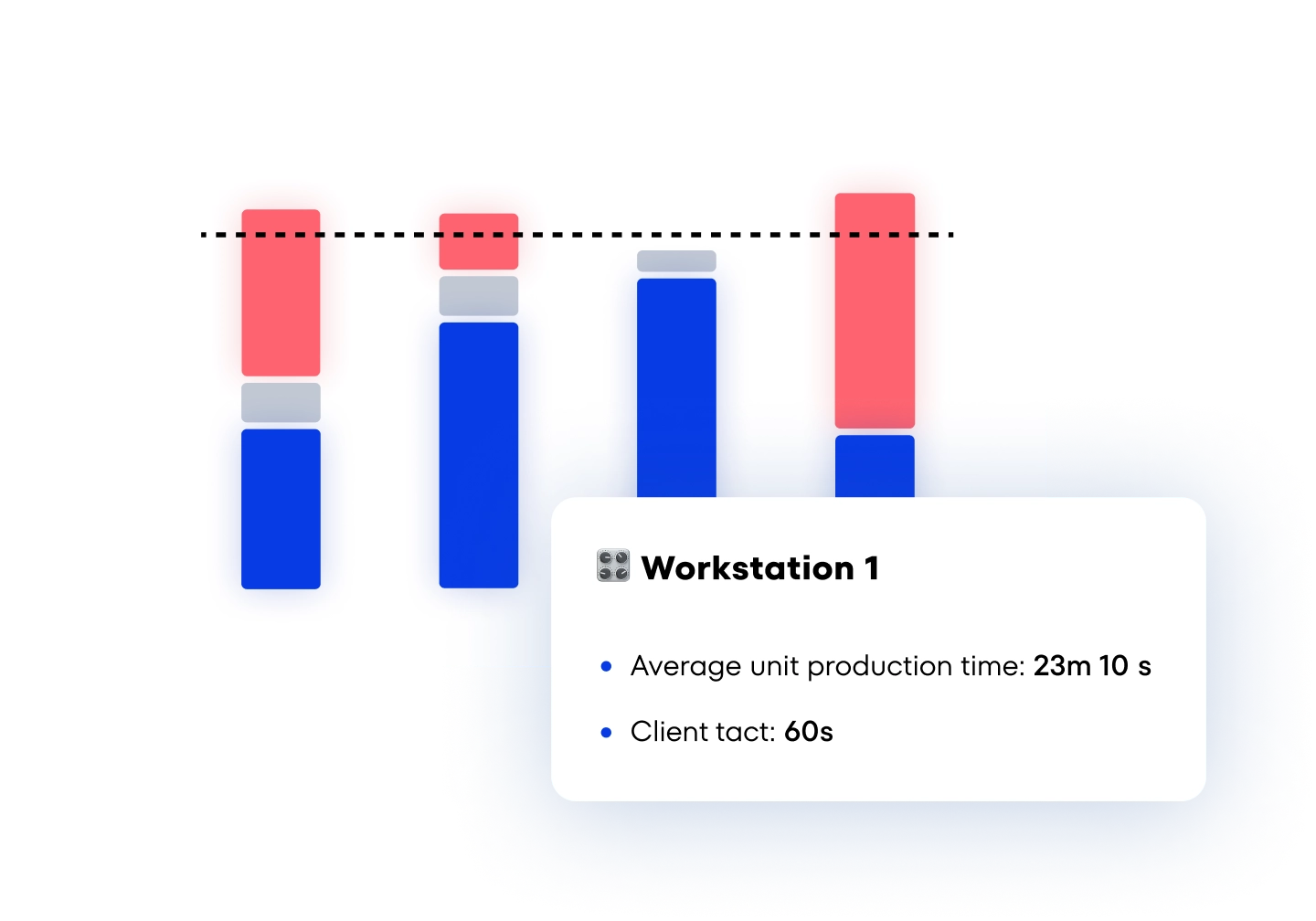
User-Centric Design & Feedback Integration
The project adopted a user-centric design approach, involving end-users in the consultation process and gathering their feedback. This ensured that the software was not only optimizing mundane tasks but also addressing the specific needs and preferences of the people who would be using it daily.
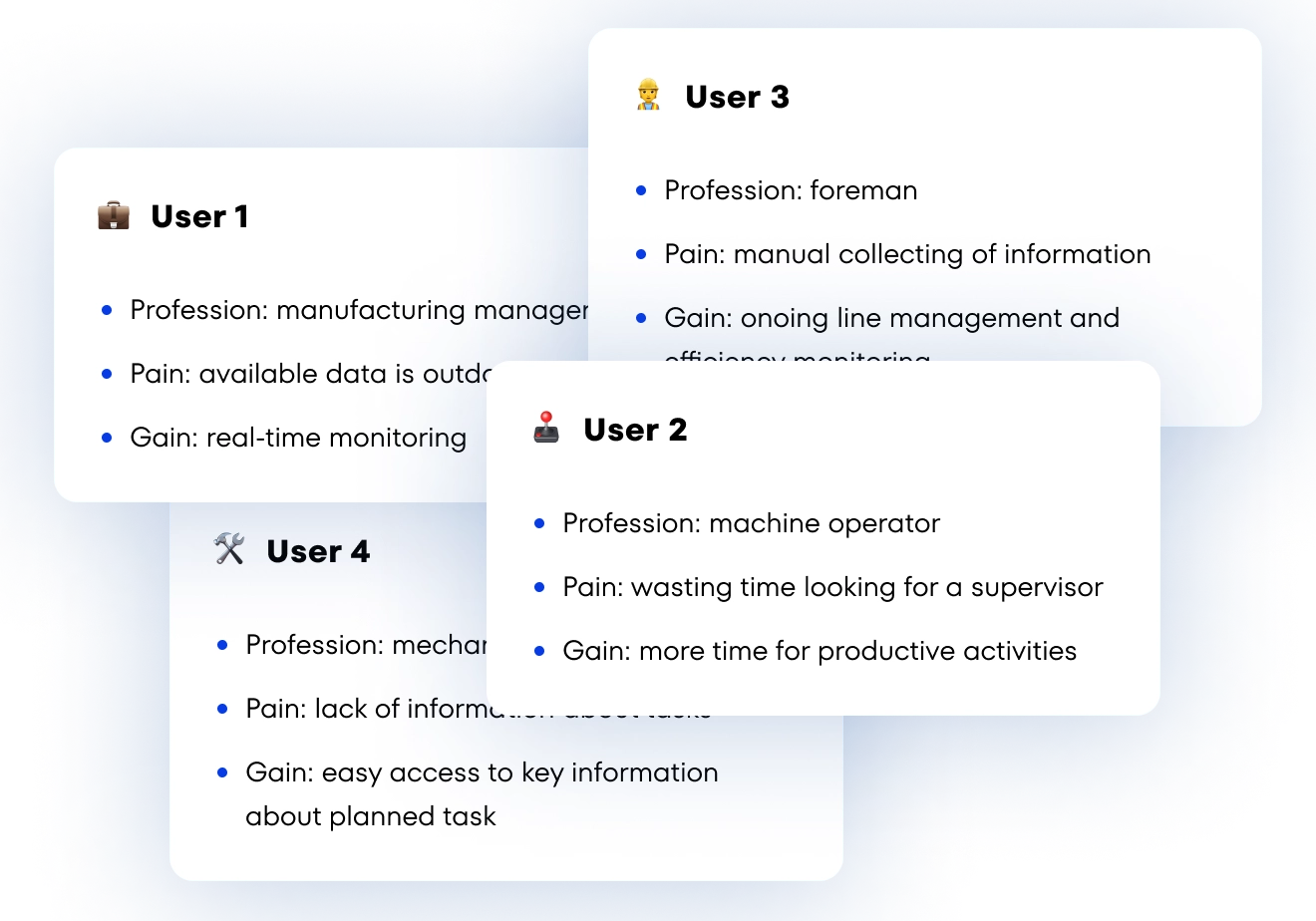
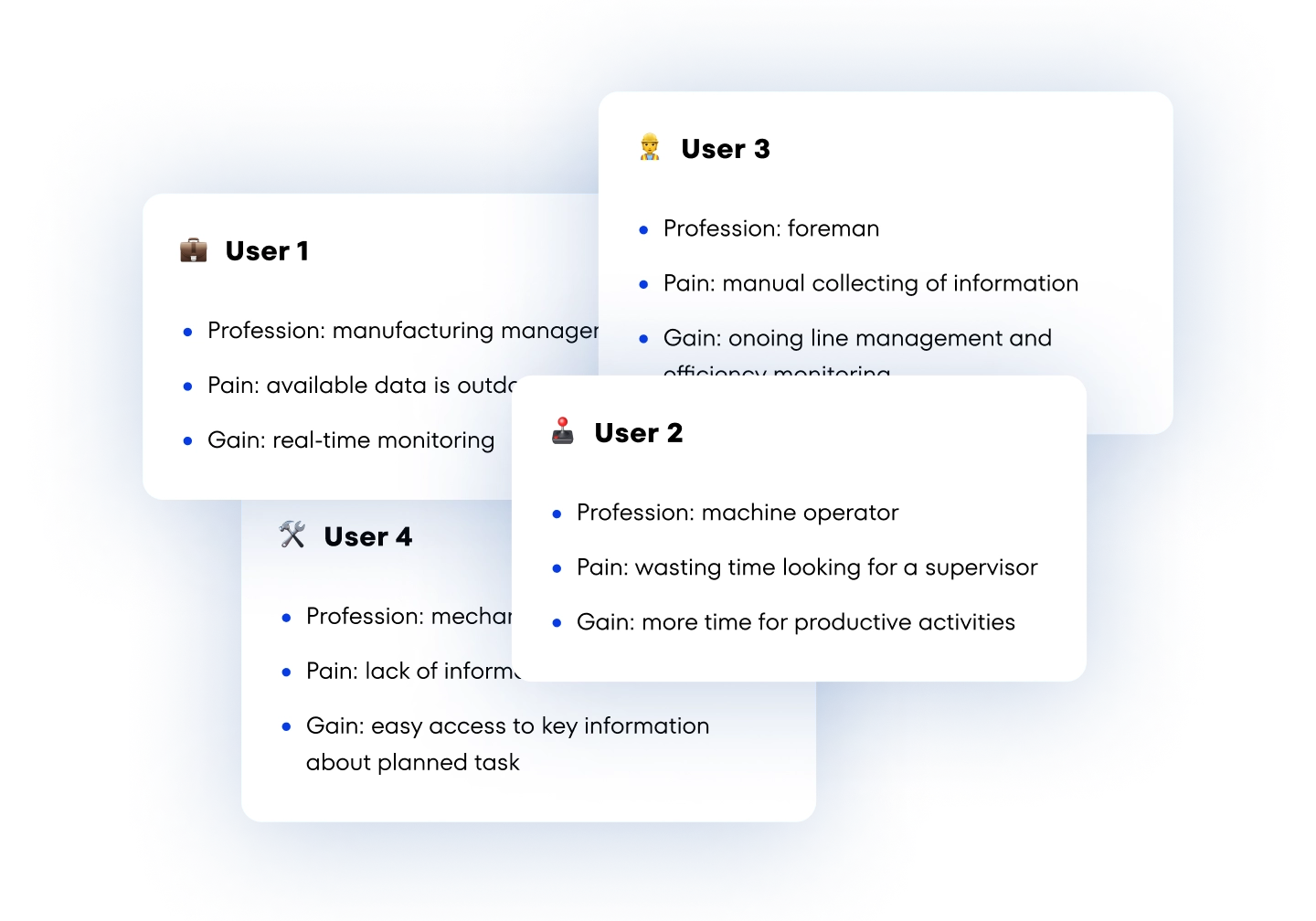
Collaborative Development & Iterative Improvement
The team worked closely with the client, ensuring that the product development was a collaborative effort. This cooperation extended beyond writing code; it involved active engagement during system implementation, considering both technical and functional feedback from the client, and continuously refining the product based on user acceptance tests.
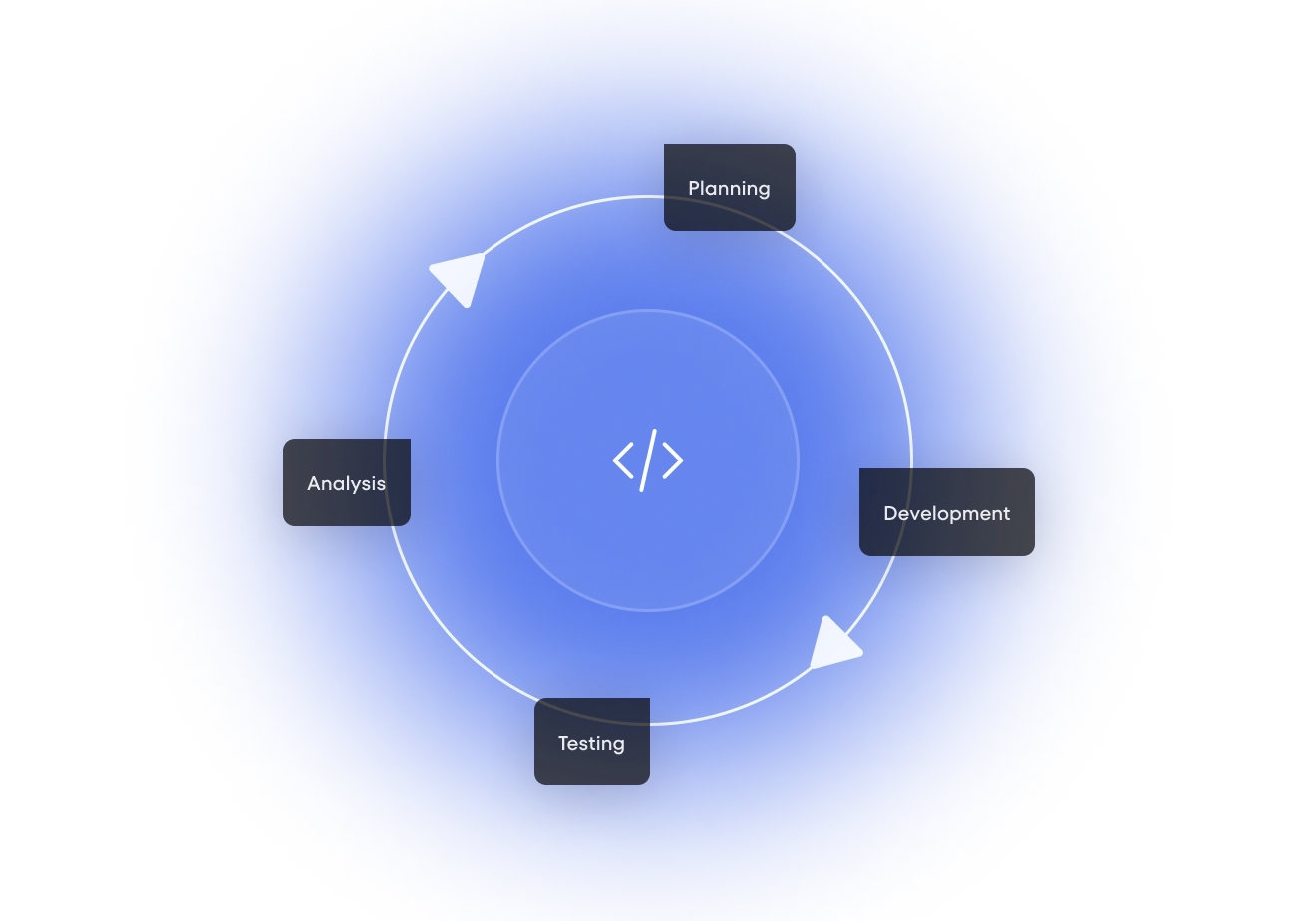
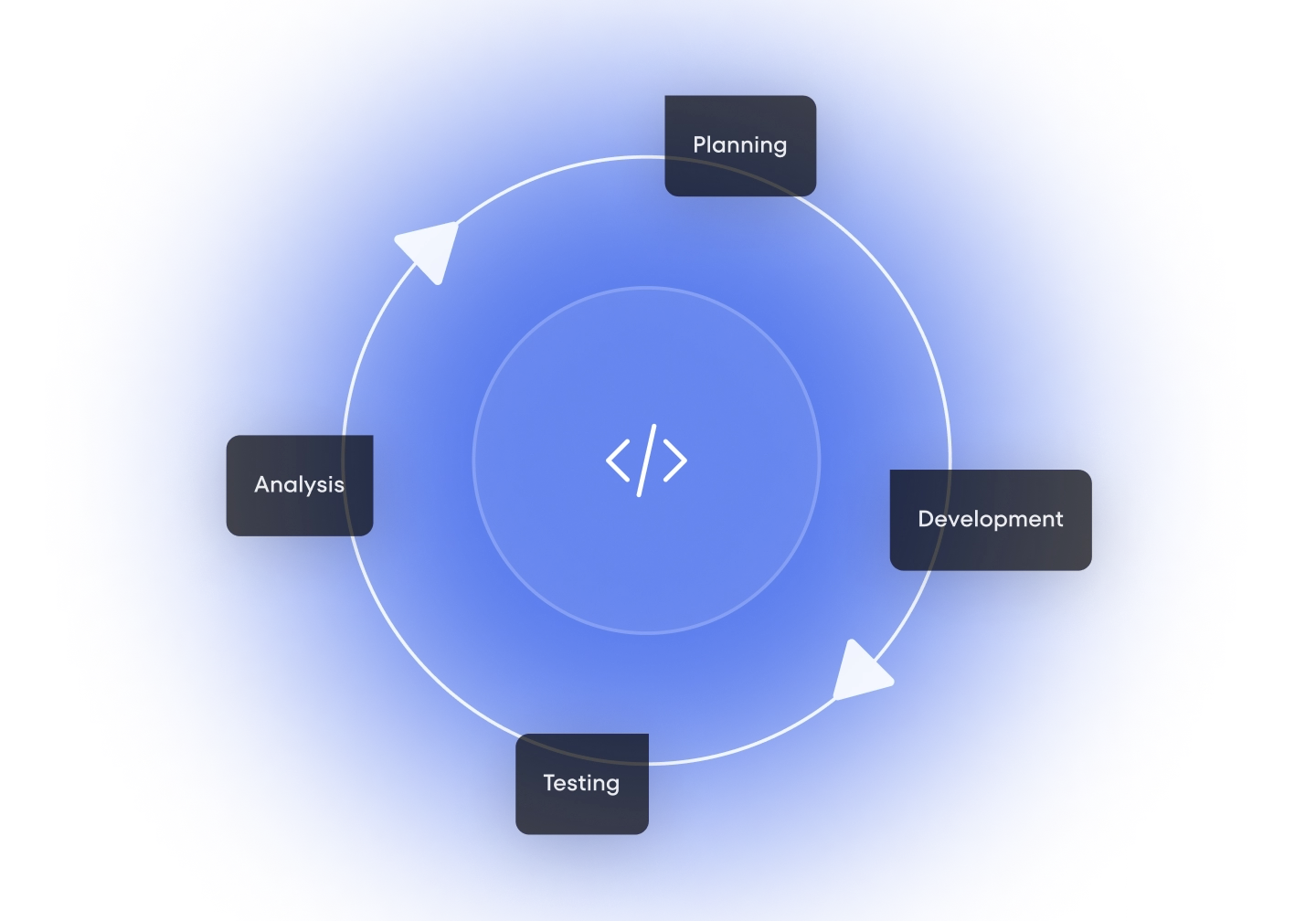
Hands-on Involvement & Detailed Planning
The team’s approach was hands-on, starting with on-site visits and extensive workshops with all stakeholders involved in the production. This immersive approach, coupled with detailed planning and preparation, facilitated a deep understanding of the industry, allowing for the creation of accurate designs and functions tailored to the end-user’s needs.
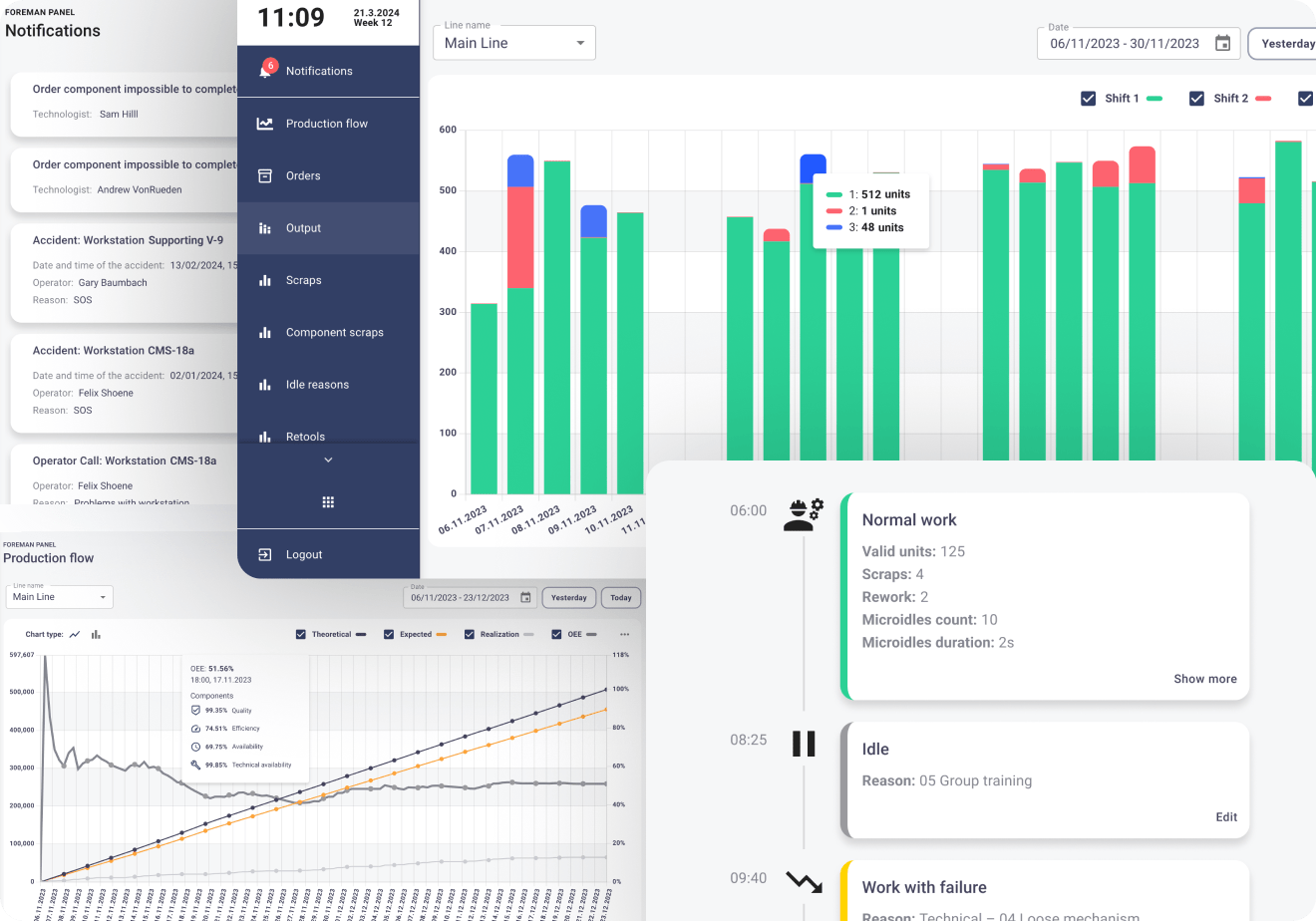
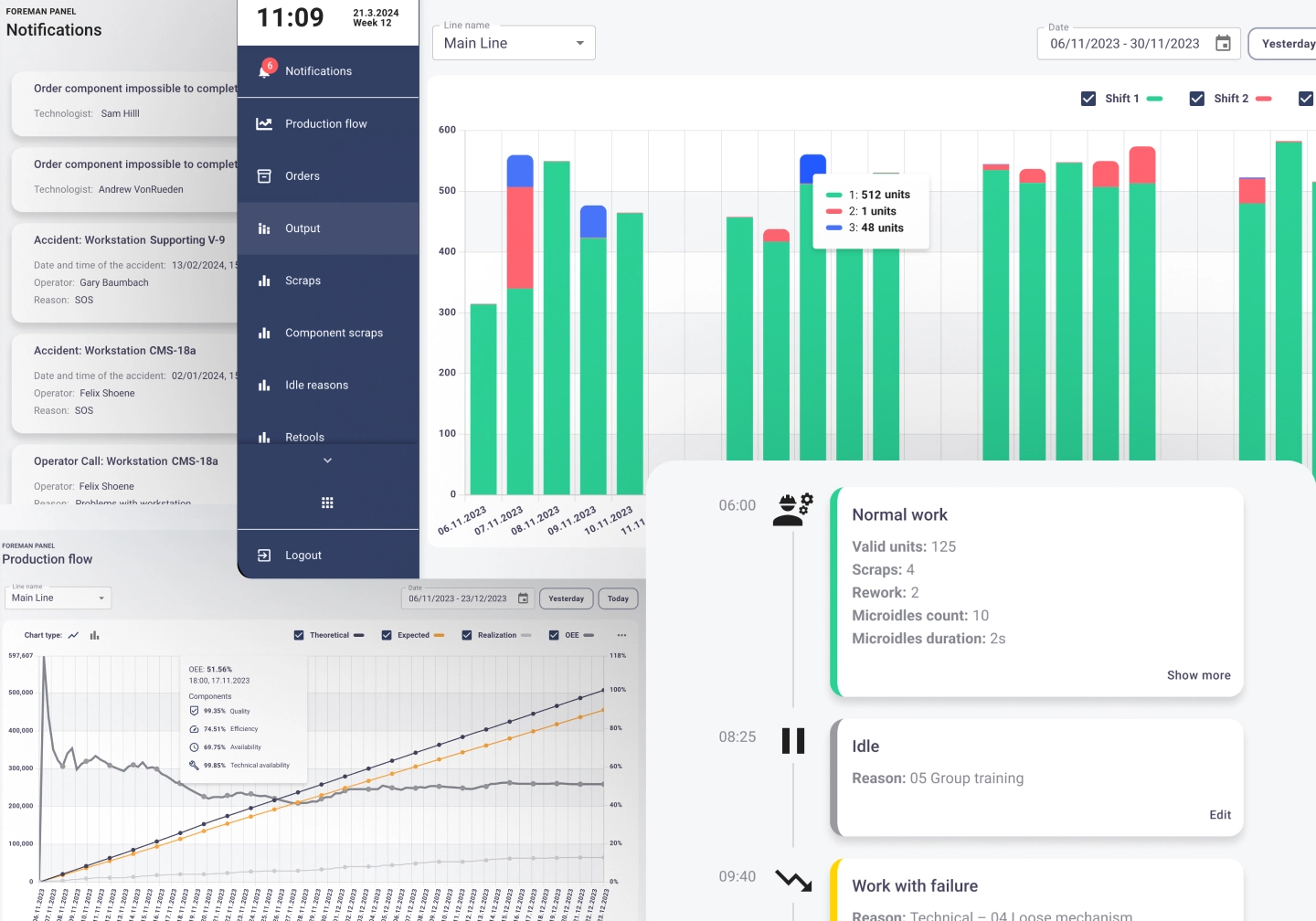
Technological Innovation & MVP Development
The approach also emphasized technological innovation. After an extended discovery period, which included visualizing the product through mockups and prototypes, the team deployed its expertise in .NET, React.js, and TypeScript to build a robust MVP (Minimum Viable Product). This MVP was not only ready to use but also scalable, keeping in mind the potential for hosting in different environments, such as on-premise infrastructure or cloud.
Check Kanri Soft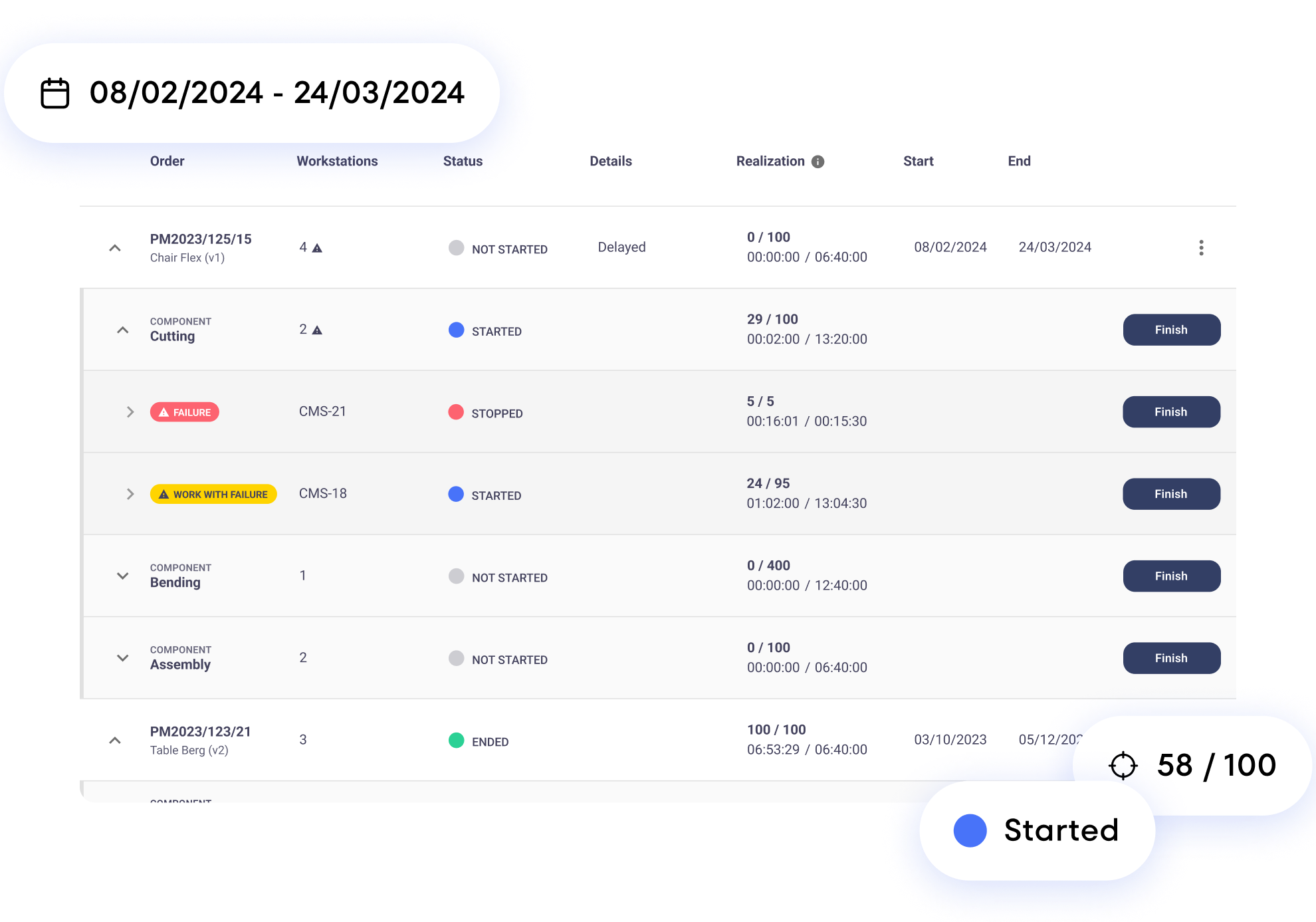
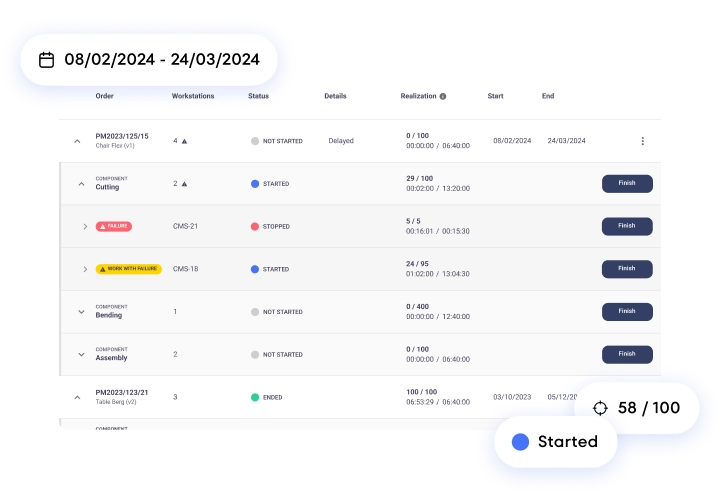
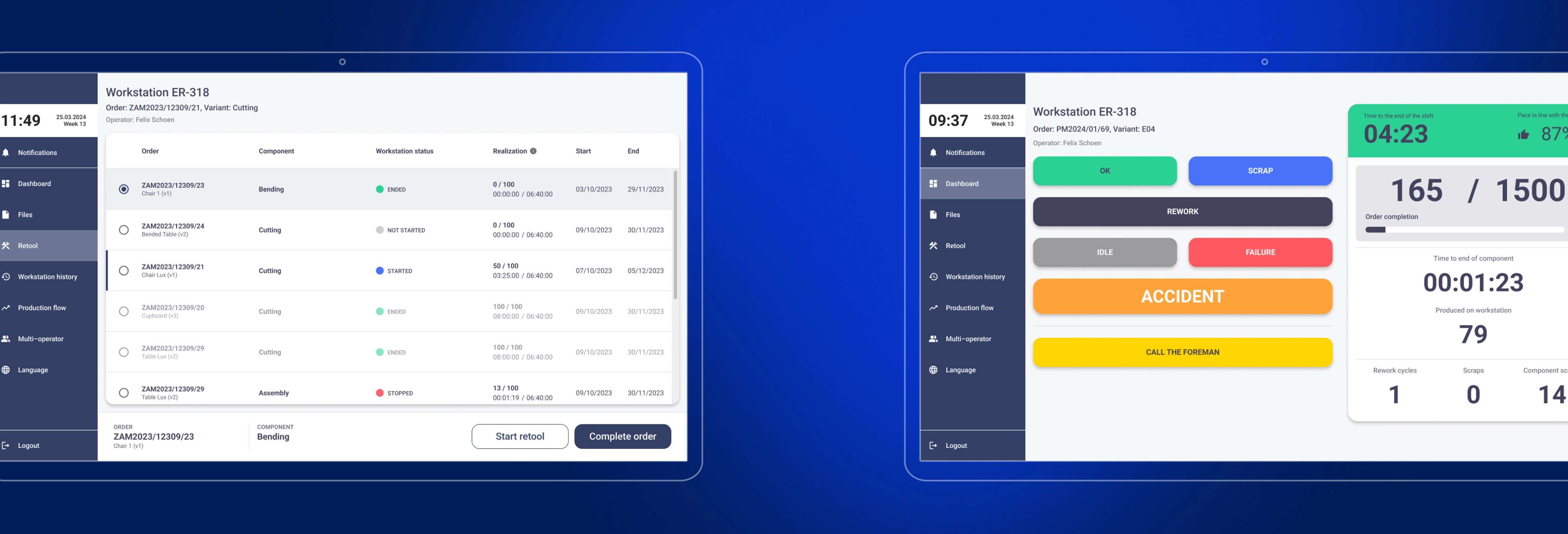
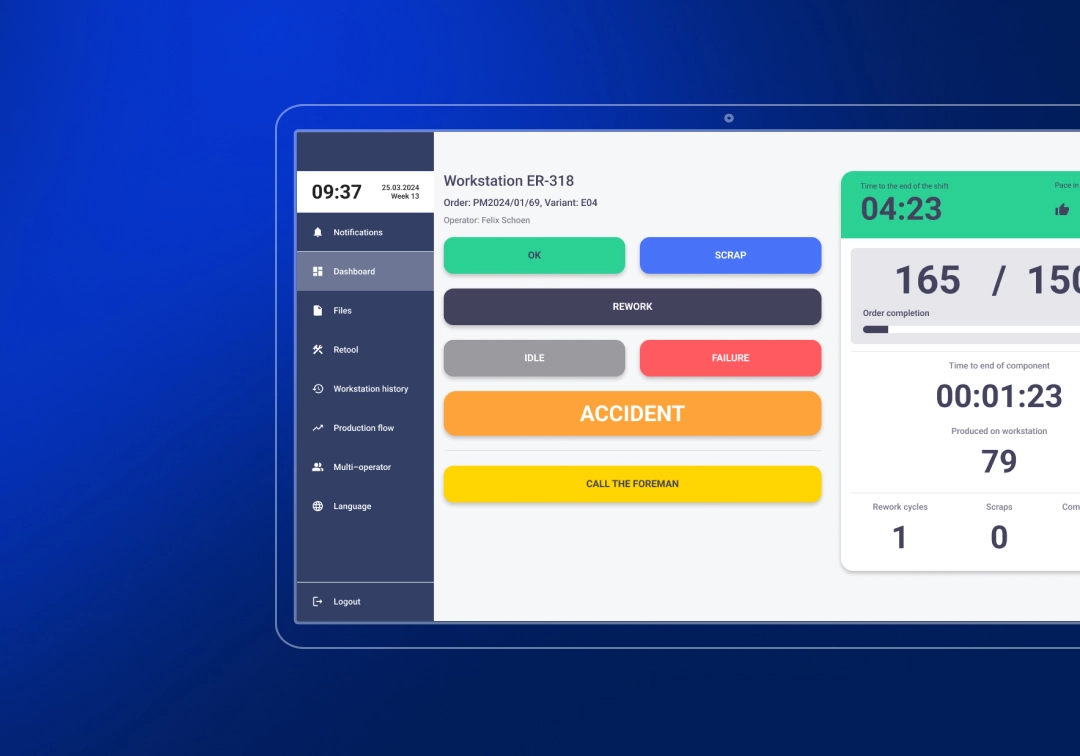
Outcome
The cooperation with Kanri Soft has yielded substantial benefits for the industrial and manufacturing sectors, significantly optimizing processes and reducing costs.
Kanri Soft’s application, by automating the data collection from machines and operators, has facilitated the elimination of paper document circulation in production, streamlining data availability for managers and contributing positively to environmental conservation.
Facts & Numbers
16%
The time of production workers is occupied by activities that do not create value for the customer.
30%
Unproductive working time can be saved thanks to the implementation of Knari software.
9/10
Is the assessment of Kanri Soft by managers on a 10-point scale.
1 Month
Is how long it takes to implement the Kanri Soft system in production.
Before investment we have asked CSHARK to fully comercially lead product discovery workshop, build product backlog and estimation. This services were delivered on such a high level of profesionalism that we have decided to ask CSHARK’S board to engage in our idea strategically.
As they have lead for us the workshop and understood well the idea and saw a full potential of the product, they have decided to trust us.
Grzegorz Gołaś
CEO at Kanri
Collaboration
Machine operators, foremen, and maintenance managers have immediate access to crucial information about the current state of production. They can easily track the number of units produced, verify the proper functioning of systems, and identify any production downtimes.
Foremen receive timely notifications about any accidents or production hiccups, enabling them to react promptly and maintain the flow of production.
Mechanics are well-informed about maintenance requirements, ensuring that they can plan and execute necessary work without delays, keeping the machinery in optimal condition.
Shift supervisors access comprehensive shift statistics, current stock numbers, and the state of machines. This information is presented in colorful, easy-to-understand graphs, catering to their preference for visual data representation.
Innovate
With Reliable
Business
Partner
Reach to us, and let’s initiate a strategic collaboration aimed at your success.